









Medical Sector Production Systems
Since its foundation in 1974, Hekuma has installed around 5,000 systems worldwide. Systems from Hekuma work in the environment of injection molding machines. They remove freshly manufactured plastic parts, such as trays, vials and sleeves, and add further plastic parts to these in an automated assembly process to form products or preliminary products. This is often followed by further assembly and testing steps, which Teamtechnik serves with its systems.
Our systems meet all the current market requirements for the production, processing and assembly of high-volume medical parts. We focus on platform machines with a high level of standardized automation steps, but also offer customized solutions for your product. Sophisticated and seamlessly integrated proven processes enable an efficient production.
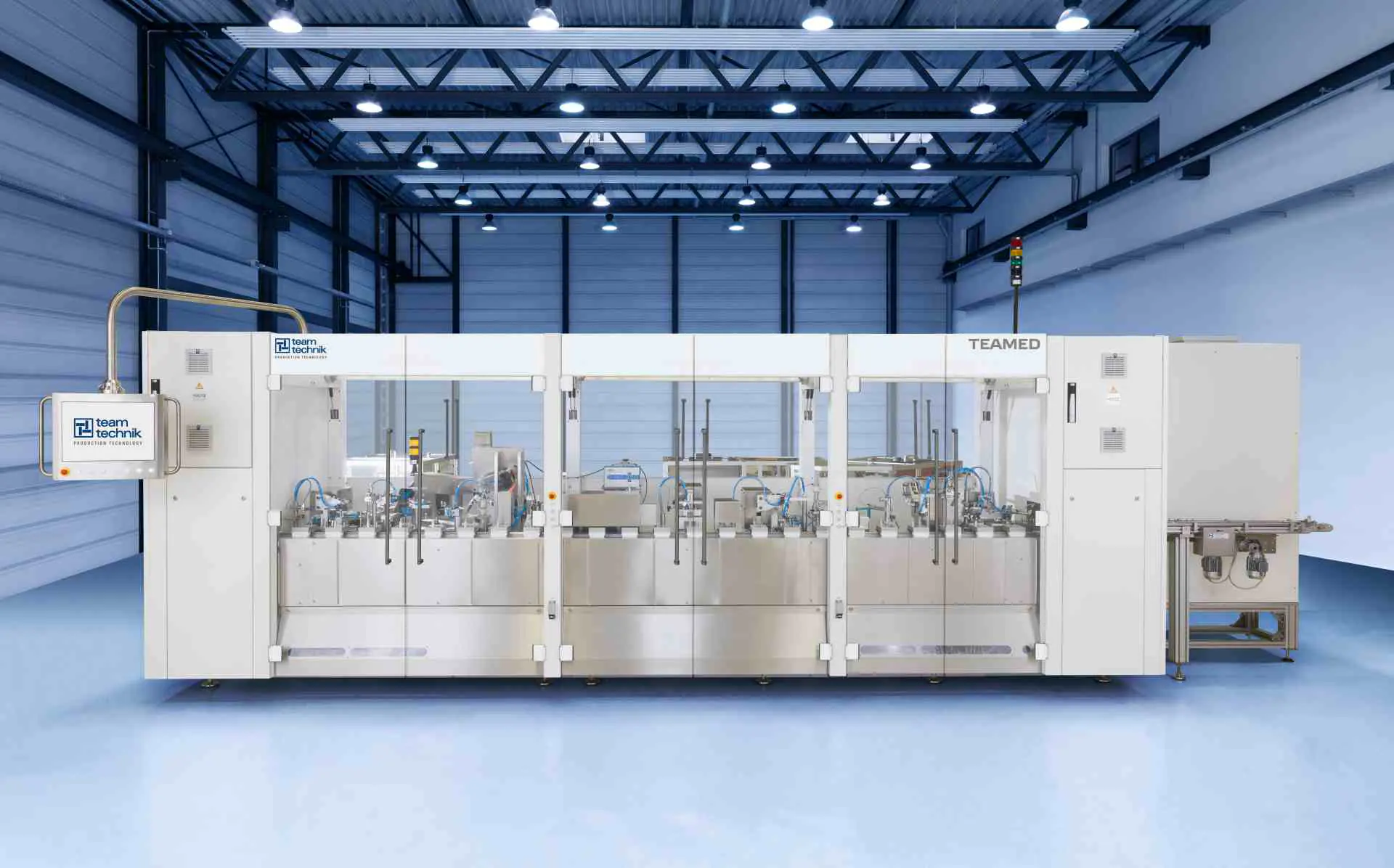
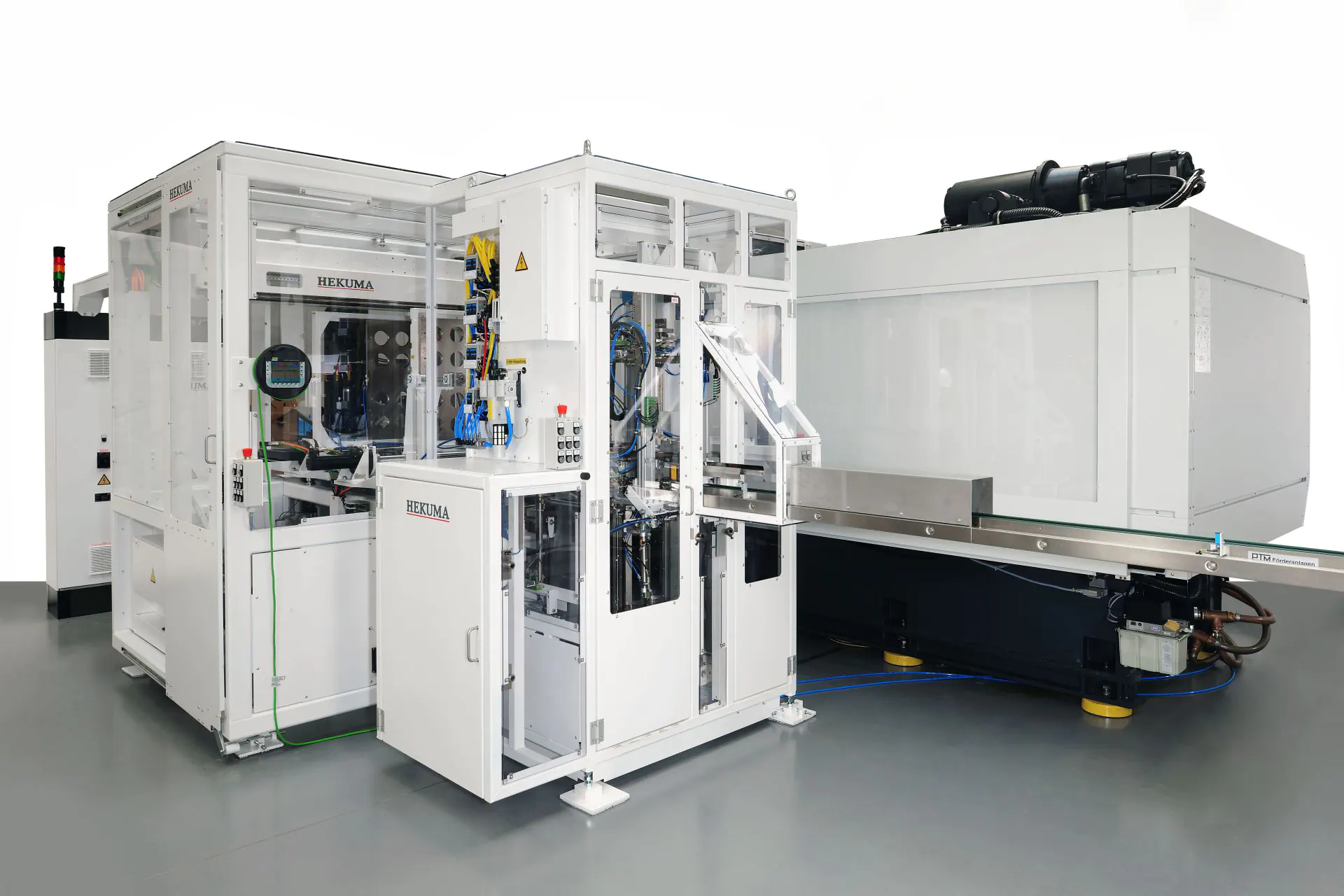
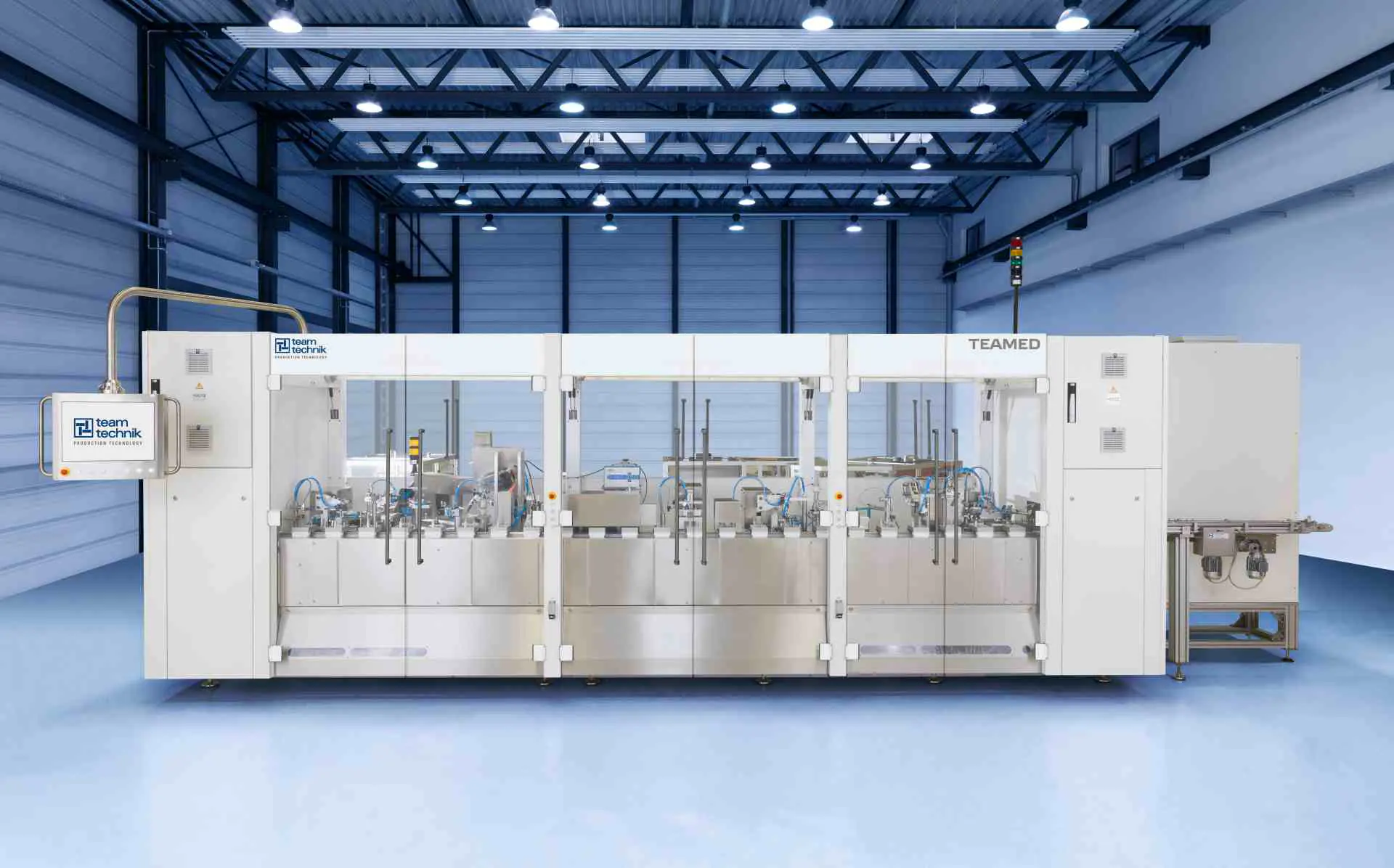
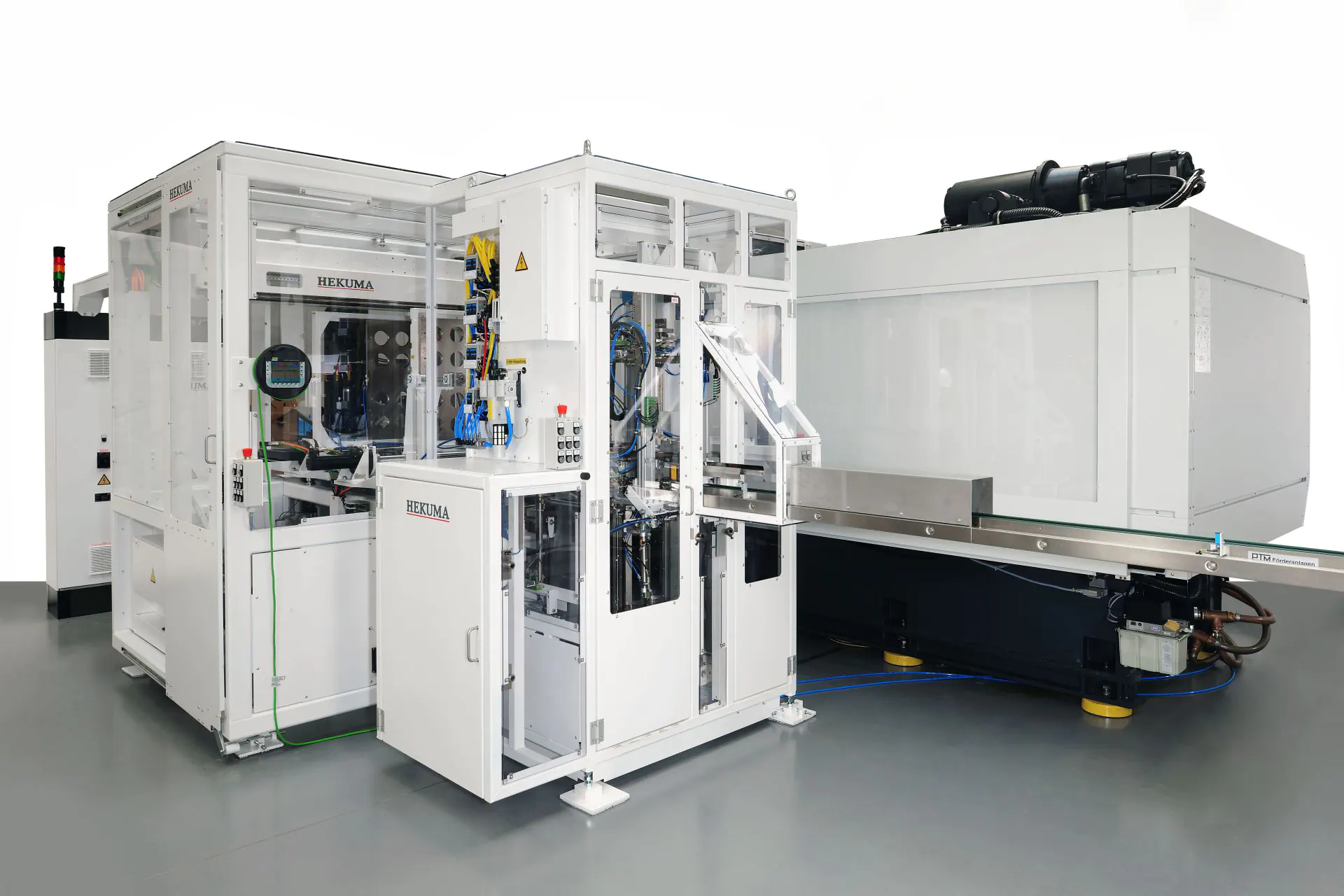
Portfolio:
Consultation & concept engineering
Optimized product automation requires that requirements are closely coordinated with a view to the product itself, the production environment and the production technology. We add our many years of experience in engineering automation systems to this coordination process. The final result is an optimized production concept that is customized perfectly to fit your needs.
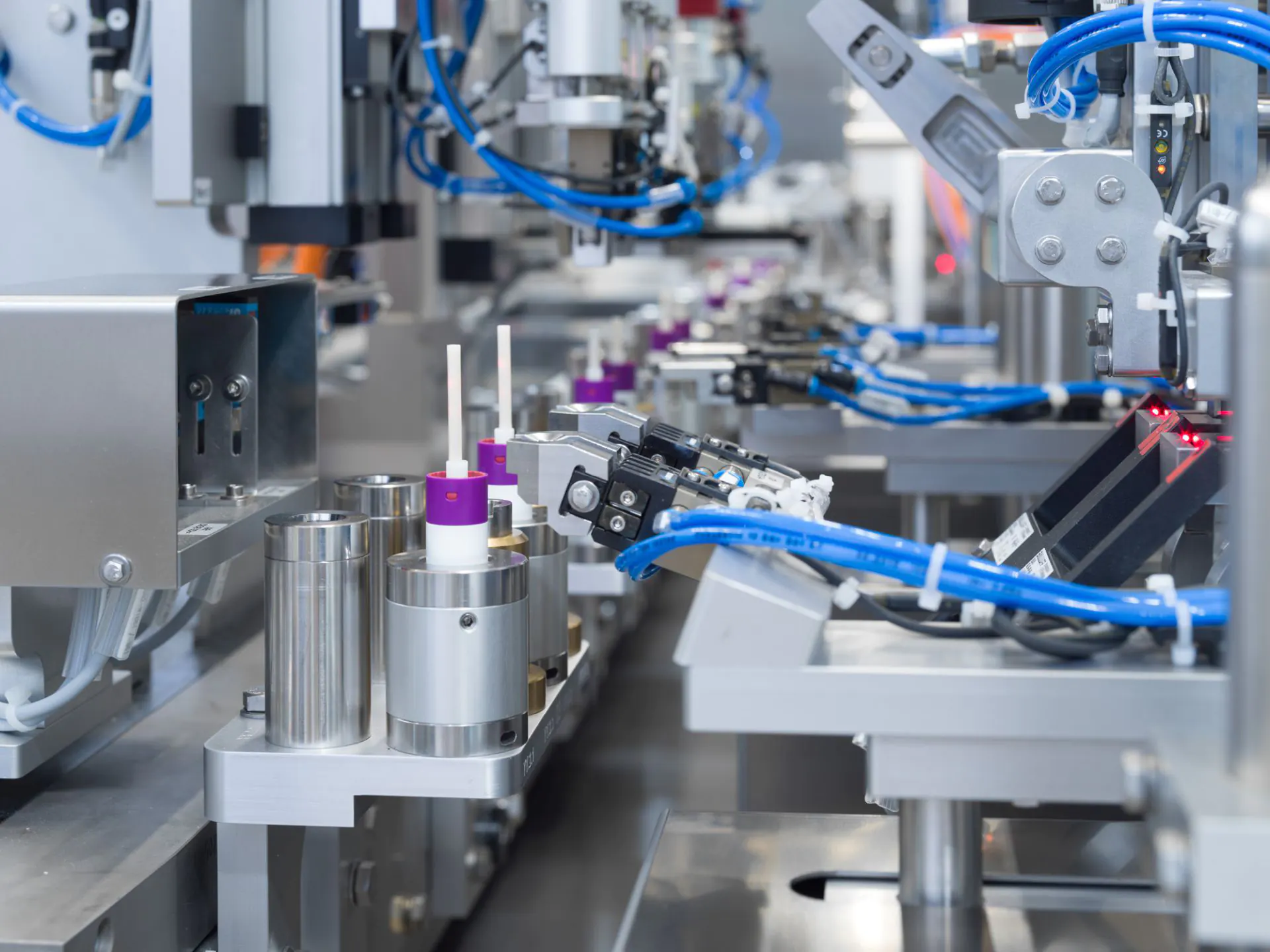
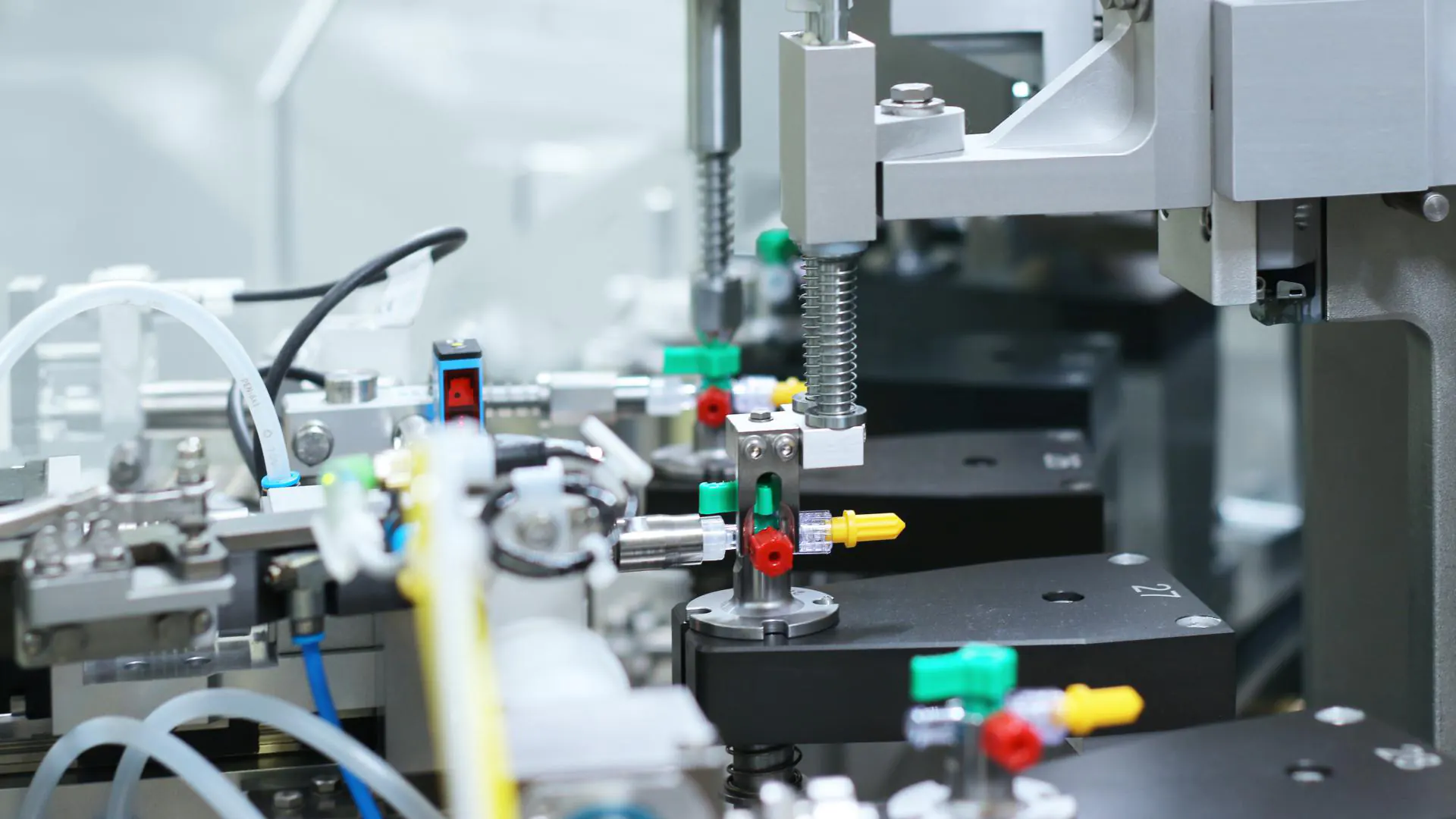
Clean room solutions
Medical injection molded products are typically manufactured in clean room environments. Our systems ensure the best possible utilization of this high-cost production area. They are designed for high cavity quantities, shortest cycle times and highest availability rates. In many instances, our customers can fall back on our proprietary integrated clean room concept. This makes relocating the entire production system to a clean room environment completely unnecessary.
Documentation & qualification
When medical products are introduced to the market, this requires detailed qualification and validation processes in accordance with European and local regulations and standards, MPG, FDA, GMP and GAMP. Our systems are developed, engineered and produced with these requirements in mind. Software modules that are installed have already been validated in advance, making a work-intensive software validation significantly easier. For optimum support, the HEKUMA quality management has been expanded to conform DIN EN ISO 13485:2012.
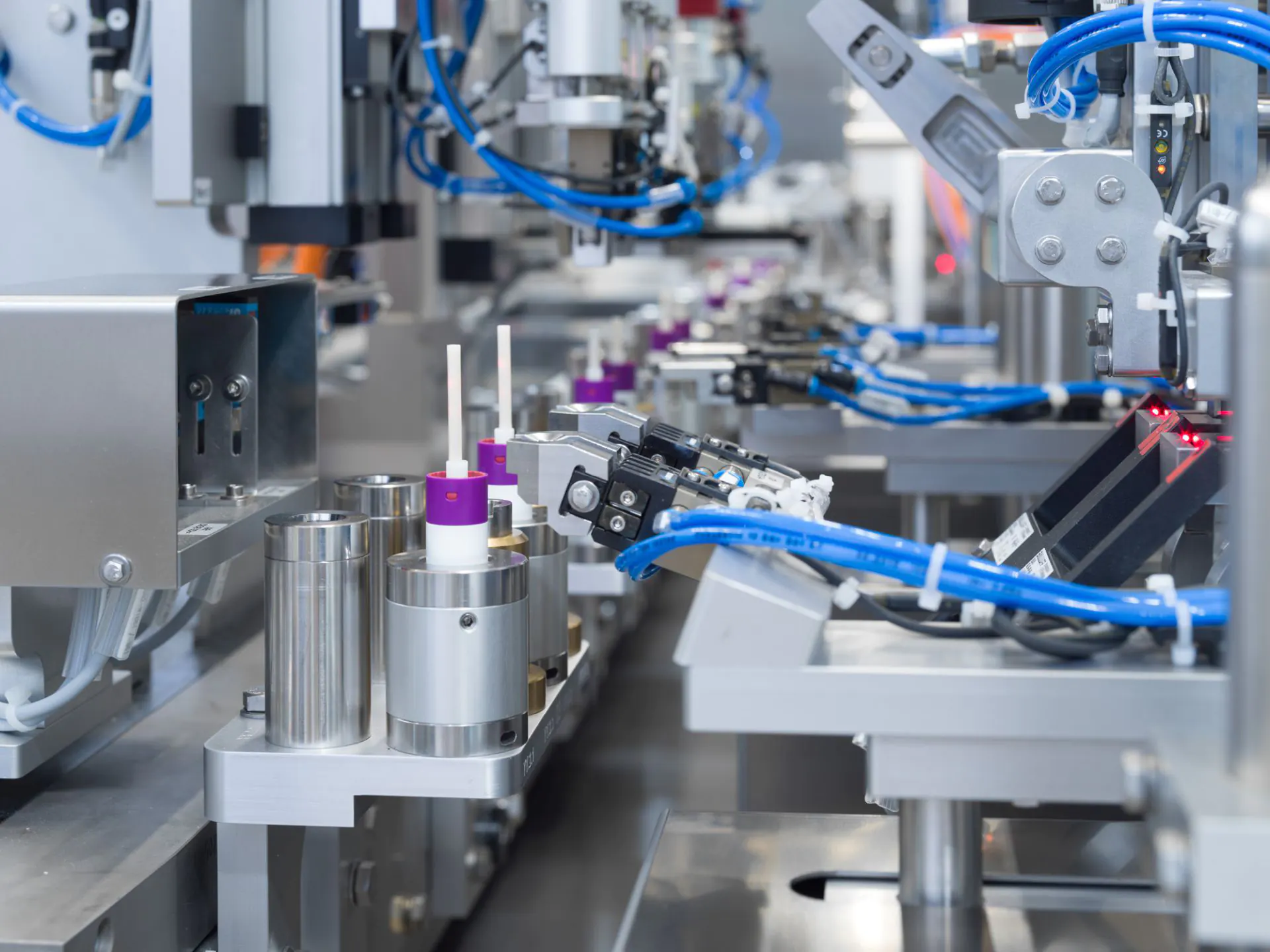
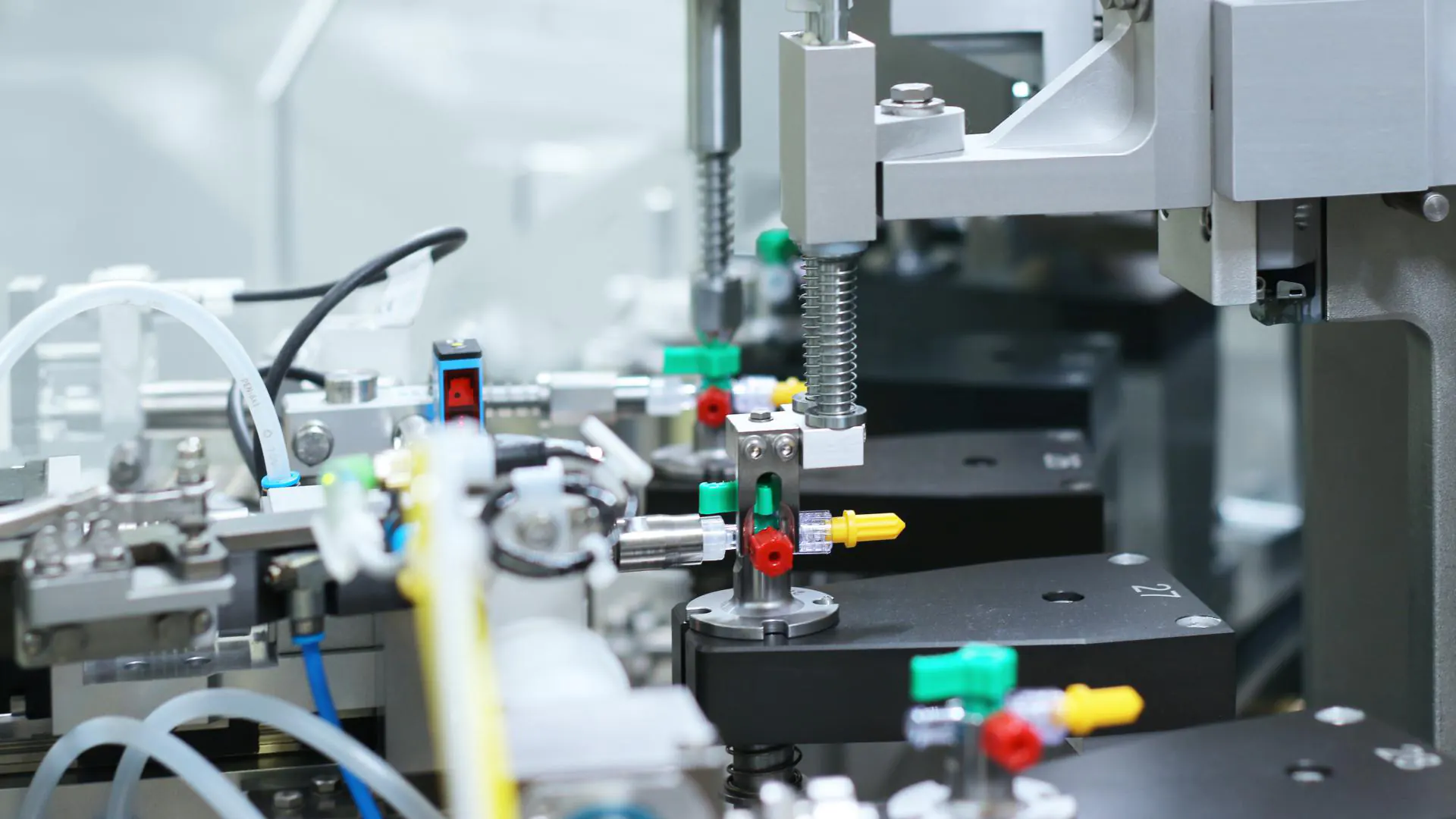
Integrating IMM and IM
Generally, we integrate the injection molding machine and the injection mold right here in our plant. This allows the entire production process to be fully vetted before the complete system is set up in your clean room production environment. This way, we can optimize processes and cycle times well in advance. This reduces the time needed for installation and initial set-up.
Integration of external systems
A fully integration of external systems, such as lasers, printers and packaging machines, into the overall concept allows the operation via one control system. Of course, it always depends on the external systems. Its advantage is that you get a closed system that is optimally coordinated.